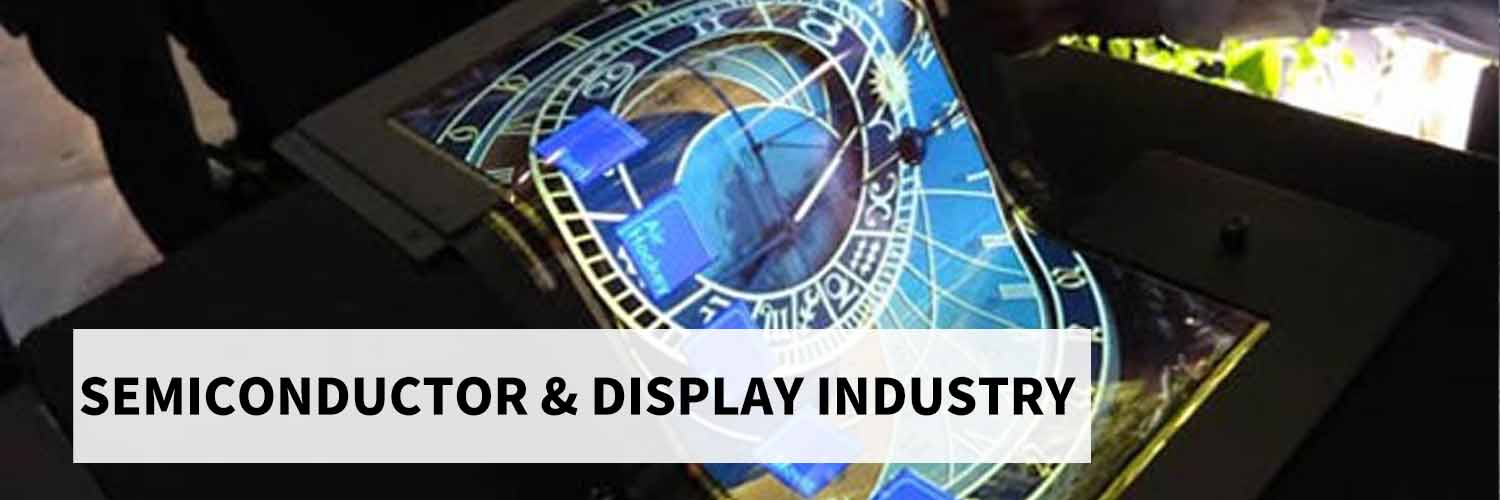
Semiconductor & Display Industry
Industry Overview
The semiconductor and display industry stands at the core of the modern digital world, powering everything from smartphones and televisions to electric vehicles and AI-driven devices. As device miniaturization and performance requirements grow, manufacturers face increasingly stringent demands on precision, cleanliness, and efficiency.
Laser technology, with its non-contact, ultra-precise, and contamination-free characteristics, has become a key enabler in front-end wafer processing, back-end packaging, and flat panel display (FPD) production. Its ability to achieve micro-level accuracy, selective material interaction, and minimal thermal impact makes it ideal for this high-spec sector.
Industry Challenges
Extremely fine structures and micron-level tolerances in wafer and panel processing
Diverse and delicate materials (e.g., silicon, glass, polyimide, OLED layers) prone to damage
Zero tolerance for contamination or residue in cleanroom environments
Increasing demand for flexible displays and micro-LEDs, requiring ultra-precise processing
Growing production automation and data traceability demands
Laser Solutions for Semiconductor & Display Manufacturing
Laser Marking Solutions
Applicable Applications: Wafer ID marking, IC packaging codes, PCB traceability, FPD substrate tracking
Value: Non-damaging, high-contrast micro markings that ensure lifetime traceability in ultra-clean environments
Recommended Products: UV Laser Marking Machine, Green Laser Marking System
Laser Cutting / Scribing Solutions
Target Materials: Glass panels, polyimide layers, OLED films, silicon wafers
Advantages: Ultra-fine kerf, smooth edges, minimal heat impact, and clean cutting
Recommended Products: UV Laser Cutting Machine, Femtosecond Laser Scribing System
Laser Cleaning Solutions
Use Cases: Pre-bond surface cleaning, oxide removal, residue cleaning from wafers or masks
Benefits: No contact or chemical use, ideal for cleanrooms, precise and selective area cleaning
Recommended Products: UV/Femtosecond Laser Cleaning Machine, Automated Precision Cleaning Platform
Laser Drilling / Structuring Solutions
Applications: Via hole drilling in PCBs, microchannel fabrication in MEMS, patterning on ITO glass
Advantages: High-speed, micron-level precision, scalable to production lines
Recommended Products: UV Laser Micro-Drilling System, Picosecond Structuring Platform
Why Choose Us?
Extensive Industry Experience: Trusted by global semiconductor and display manufacturers
Cleanroom Compatibility: Equipment built for Class 100–1000 cleanroom environments
Modular Design: Custom laser modules or full systems based on line integration needs
Vision-Assisted Control: AI + machine vision alignment and real-time feedback
Traceability Ready: Fully compatible with MES, barcode/QR/NFC traceability systems
Application Examples
PROJECT | LASER PROCESS |
---|---|
Wafer ID code marking | UV laser marking |
OLED panel glass cutting | UV laser cutting |
Surface cleaning before bonding | Femtosecond laser cleaning |
Via hole drilling in IC substrate | UV laser drilling |
ITO patterning on display glass | Picosecond laser structuring |
Industry Trends
Rise of Advanced Packaging: Laser processes are essential in 3D ICs, chiplets, and FOWLP
Flexible & Miniaturized Displays: Laser cutting and structuring enable flexible OLEDs and micro-LED tech
Green, Dry Processes Preferred: Lasers meet ESG demands with no consumables or chemical waste
Precision + Automation Synergy: Integration of lasers into fully automated fabs is accelerating
Our Cooperation Models
Provide complete machine solutions or customized modular units
Support technical assistance, installation & commissioning, and training services
Offer OEM/ODM cooperation models to meet industry-specific requirements
Contact Us for Customized Laser Solutions
Whether you’re building a new cleanroom production line, upgrading a wafer fab, or integrating precision laser systems into flexible display production, our engineering team can tailor complete solutions to fit your materials, processes, and capacity goals—ensuring ultra-clean, high-speed, and future-proof manufacturing.