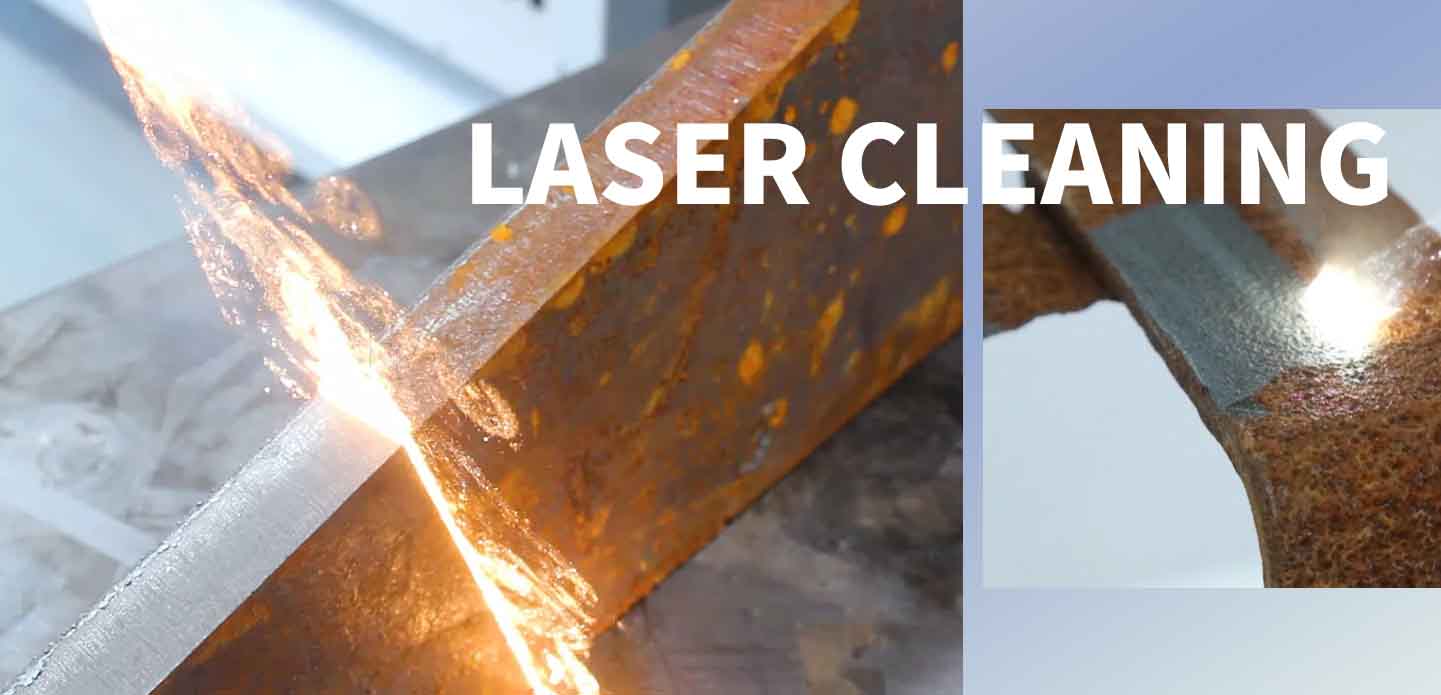
In recent years, the demand for efficient, eco-friendly, and non-damaging cleaning solutions in industrial settings has given rise to a new generation of surface treatment equipment—pulse laser cleaning machines. These systems use ultra-short, high-energy laser pulses to remove contaminants such as rust, paint, oil, oxide, and residue from various surfaces, without the need for chemicals, abrasive materials, or physical contact.
Unlike traditional cleaning methods, pulse laser cleaning offers precise control, low thermal impact, and minimal material loss, making it an ideal solution for industries that require both performance and surface integrity.
1. What Is a Laser Cleaning Machine?
A pulse laser cleaning machine is a non-contact cleaning system that uses short-duration, high-peak-power laser pulses to selectively remove surface impurities. The laser energy is absorbed by contaminants or coatings, causing them to rapidly expand and break away from the substrate, while the underlying material remains largely unaffected.
Key Characteristics:
Pulse Width: Typically in the nanosecond to microsecond range
Laser Type: Fiber, Nd:YAG, or MOPA (Master Oscillator Power Amplifier)
Power Range: 20W to 2000W depending on the application
Cooling System: Air-cooled (portable) or water-cooled (high-power)
2. How Pulse Laser Cleaning Works
The principle of pulse laser cleaning relies on the difference in absorption between the contaminant and the base material. When the laser pulse hits the surface:
The contaminant absorbs energy more readily than the substrate.
The localized temperature rises rapidly, creating a plasma or shockwave.
This leads to thermal expansion, vaporization, or mechanical disintegration of the contaminant.
The residue is ejected without harming the surface underneath.
Because the energy is delivered in extremely short bursts, there is minimal heat conduction, reducing the risk of warping, melting, or damaging sensitive materials.
3. Advantages of Pulse Laser Cleaning Machines
Feature | Benefit |
---|---|
Non-contact process | No mechanical abrasion or deformation |
Eco-friendly | No need for solvents, acids, or sandblasting media |
Precision control | Can target specific contaminants without affecting nearby surfaces |
Minimal maintenance | Fewer moving parts, no consumables |
Automatable | Easily integrated into robotic arms and CNC systems |
For industries like aerospace, automotive, energy, and electronics, these advantages translate into better quality, lower cost, and higher productivity.
4. Common Applications of Pulse Laser Cleaning
Rust and Oxide Removal
Pulse laser systems can clean oxidation from steel, iron, and aluminum components with high precision, often used in shipbuilding and rail repair.
Paint and Coating Stripping
They can remove paint layers from automotive or aerospace parts without damaging the substrate, preserving geometry and surface finish.
Oil, Grease, and Mold Release Agent Removal
In plastic or rubber manufacturing, they clean molds before production runs.
Welding Pre- and Post-treatment
Used to remove oxide or contamination before welding and clean burn marks or spatter afterward.
Cultural Heritage and Restoration
Museums and conservators use pulse lasers to delicately clean marble, bronze, and frescoes.
5. Pulse vs. Continuous Laser Cleaning
Parameter | Pulse Laser Cleaning | Continuous Laser Cleaning |
---|---|---|
Precision | High | Medium |
Heat Input | Low | High |
Material Compatibility | Sensitive and delicate surfaces | Robust metal surfaces |
Cost | Higher (per watt) | Lower |
Surface Damage Risk | Minimal | Possible on thin materials |
Pulse laser cleaning is preferred where surface sensitivity, precision, and minimal damage are key, while continuous laser cleaning is better for bulk rust or paint removal on thick, industrial-grade metals.
6. Choosing the Right Pulse Laser Cleaning Machine
When selecting a system, consider:
Type of contamination (rust, oil, oxide, paint)
Material type (metal, plastic, ceramic, stone)
Surface area and complexity
Required mobility (handheld vs. fixed)
Power level (e.g., 100W for light rust, 1000W+ for thick coatings)
Integration (standalone or inline automation)
Many manufacturers now offer portable, plug-and-play handheld pulse laser cleaning machines, often weighing less than 20 kg and ideal for field maintenance or workshop use.
7. Future Trends in Pulse Laser Cleaning (2025 and Beyond)
Intelligent Laser Control
AI-assisted control systems adjust pulse energy and scanning speed in real-time based on surface feedback sensors.
Energy Efficiency Optimization
Advanced power modulation reduces energy waste and extends equipment lifespan.
Compact High-Power Systems
Development of air-cooled 1000W+ pulse lasers will enable high-throughput cleaning in smaller form factors.
Multi-Axis Robotic Integration
Laser cleaning heads are now mounted on robotic arms with 6-axis movement for cleaning complex geometries with absolute precision.
8. Environmental and Regulatory Benefits
Because pulse laser cleaning machines operate without solvents or secondary waste, they help companies:
Comply with ISO 14001 environmental management systems
Reduce VOC emissions
Minimize disposal costs for hazardous materials
Improve workplace safety and cleanliness
This makes them ideal for manufacturers aiming to meet stricter ESG (Environmental, Social, and Governance) goals or government environmental mandates.
Conclusion: Why Pulse Laser Cleaning Is the Future of Industrial Surface Treatment
As industries demand faster, cleaner, and greener solutions, pulse laser cleaning machines are rapidly replacing outdated mechanical and chemical cleaning methods. Their ability to clean with surgical precision—without damaging the substrate—makes them invaluable across sectors from aviation to electronics.
Whether you’re dealing with delicate aerospace alloys or heavily oxidized structural steel, pulse laser cleaning offers a scalable, efficient, and environmentally responsible path forward.